Graders: Maintenance and Operations
3min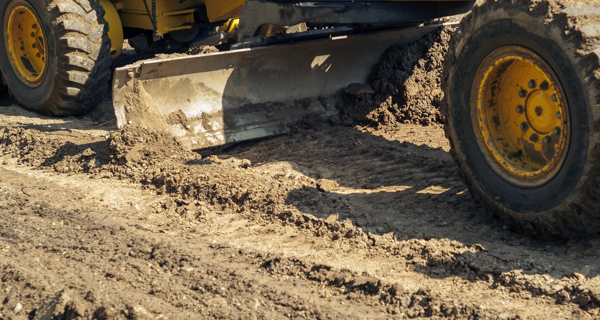
Whether it’s for roads, spreading, fine grading, earthmoving or debris clearing, graders are one of your businesses most versatile assets. So, it’s essential to keep them performing at their peak in order to get the job done.
Our Repair Manager, Andrew Brennan, and Assessing Services Manager, Dion Cooper share tips for maintaining and servicing your grader to ensure it stays in tip top condition for as long as possible.
Road Grader Blades
As the blade/s attached to the mouldboard are what comes in contact with the soil, it’s common for them to obtain some wear and tear. Attention must be given to the blades cutting edge along the bottom and dependent on your grader model, on the sides of the blade as well.
“Blades that are pitched back rather than at right angles are predisposed to wear and tear, and will need to be inspected daily and replaced often,” says Andrew.
Depending on the type of surface being prepared and how abrasive it is will dictate the time it takes for the edges of the blades to get worn down. Factors such as the angle that the edges make contact with the surface will also impact this, so all blades should be visually checked every 25 to 50 hours of operation.
Failure to maintain the blade’s edges and the bolts that keep them in place may compromise the entire mouldboard.
The blade slide, which enables the mouldboard to move efficiently on a swivel track, along with the shim glides, must also be checked. Doing this every month will assist your machine giving a smooth cut.
Scarifiers should also be kept in mind. “If you have a scarifier for rough grading, the teeth must be checked regularly and be maintained so they do not wear down to the shank or pocket,” says Dion.
Road Grader Air Filters
Air filters play an integral role in the fuel efficiency of your grader. Andrew notes that operators should “check the machine’s air filters often and be sure to clear any dirt clogging the air filters.”
Installing pre-filters will reduce the amount of dirt that may enter the air filter and will prevent the need for changing the filters as regularly. Keep watch for any ‘restricted alert’ signals, as this will alert you to any airflow issues.
Operating a Grader
“We’ve seen some claims come through as a result of operators using their grader on an inappropriate surface. It’s important to ensure the equipment and attachments you are using are designed for the job,” says Dion.
A handy tip to reduce the hydraulic pressure that can damage seals and hoses by leaving the engine idle for three to five minutes before shutting down.
It’s also important to ensure you’re using the proper blade and pitch settings for the material and project. If this isn’t done you may overwork the grader and cause it to burn excessive amounts of fuel and thrust the machine sideways.
Some things to keep in mind before, during and after operation are:
- Can the machinery move to and from an allocated work area unrestricted?
- Is there safe access for machinery to transfer product around the site?
- Will there be movement of light vehicles on and around the site?
- Are all haul roads and vehicle access roads clear and serviceable?
- Will there be a need for traffic control considerations?
General Servicing of Road Graders
There are a few routine maintenance tips that are vital to the upkeep of your grader, such as:
- Monitor the hydraulic cylinder
- Check all seals
- Regularly grease and lubricate the machine
- Ensure fluid is at correct levels
- Inspect for any leaks
- Check tyre pressure
- Cleaning and hosing away any dirt build up
- Conducting regular Scheduled Oil Sampling ( SOS analysis )
“SOS analysis allows you to get an insight into the health of your machine and the results can indicate premature bearing failure in a final drive for example, so you are able to be proactive and not reactive in repairing it.
“Cutting and inspecting filters at each service is also recommended, as this will indicate any debris that may not appear in the oil sampling,” notes Andrew.
Andrew also highlights the importance of monitoring the pressure of the tyres, as the traction affects the machine’s grade and the tread is pivotal to getting good bite on the ground.
“A half-inch deep is the absolute minimum for a grader’s tyre tread,” says Andrew.
“General servicing can also help prevent electrical fires. These can stem from eroded insulation around cables, substandard non-OEM parts incompatible with the machine, poor installation of parts by non-qualified labour and malfunctions of bearings in moving electrical parts,” says Dion.
These steps can reduce the likelihood of any downtime due to your grader being out of action for repair.
Mobile Plant Machinery Maintenance Checklist
To assist in your machine pre-checks, here’s a short checklist:
If you do find that your grader is out of action or in need of repair, contact our team for Accident Assist or to make a claim on 1800 684 669. We’ll get our experienced repair managers to get you back up and running in no time.