What is a Mobile Plant Pre-Start Checklist?
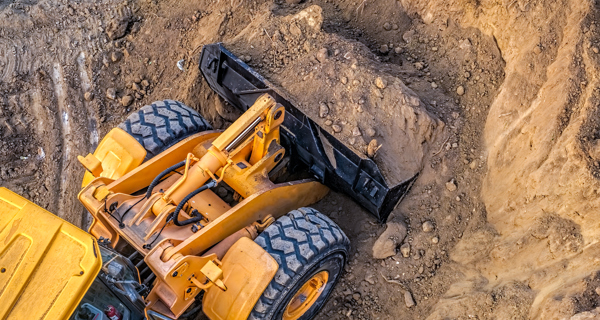
The purpose of a mobile pre-start checklist is to enhance safety, prevent equipment failures, and comply with regulatory requirements. The checklist generally includes a series of items and tasks that the equipment operator must review and verify before starting and operating the equipment. These items can cover various aspects of the equipment, including mechanical, electrical, and safety features.
This checklist provides a list of items operators must inspect and items they should also be aware of during a pre-start check each day. Operators should record that they've completed the check and any issues found. The site where the machine is to operate also plays a major role in safety and risk management. Both the machine, the operator and anyone around them could be placed in harm if the site has not been correctly assessed.
Why Use a Pre-Start Checklist?
By using a mobile pre-start checklist, organisations can systematically and consistently conduct equipment inspections, reduce the risk of mechanical failures, enhance workplace safety, and maintain compliance with relevant regulations. The use of a digital format allows for easy recording, retrieval, and analysis of inspection data. It also facilitates communication between operators, maintenance teams, and management regarding the condition of equipment.
Neglecting pre-checks can lead to equipment failures, accidents, and injuries. It may also result in increased downtime, higher maintenance costs, and non-compliance with safety regulations.
Download the Checklist
FAQs
-
Who is responsible for conducting mobile plant pre-checks?
Typically, the operator or user of the mobile plant is responsible for conducting pre-checks. This includes ensuring that the equipment is safe and in proper working condition before it is put into operation.
-
What should be done if issues are identified during a pre-check?
If issues are identified during a pre-check, the operator should report them to the appropriate personnel or maintenance team. Depending on the severity of the issue, the equipment may need to be repaired or taken out of service until it is safe to use.
-
Is training required for operators to conduct effective pre-checks?
Yes, operators should receive training on how to conduct thorough pre-checks. Training should cover the specific inspection points for the equipment they operate and emphasise the importance of reporting any issues promptly.
-
How can organisations encourage a culture of compliance with mobile plant pre-checks?
Organisations can foster a culture of compliance by providing thorough training, emphasising the importance of pre-checks, implementing easy-to-use digital tools, and recognising and rewarding operators who consistently adhere to safety protocols.